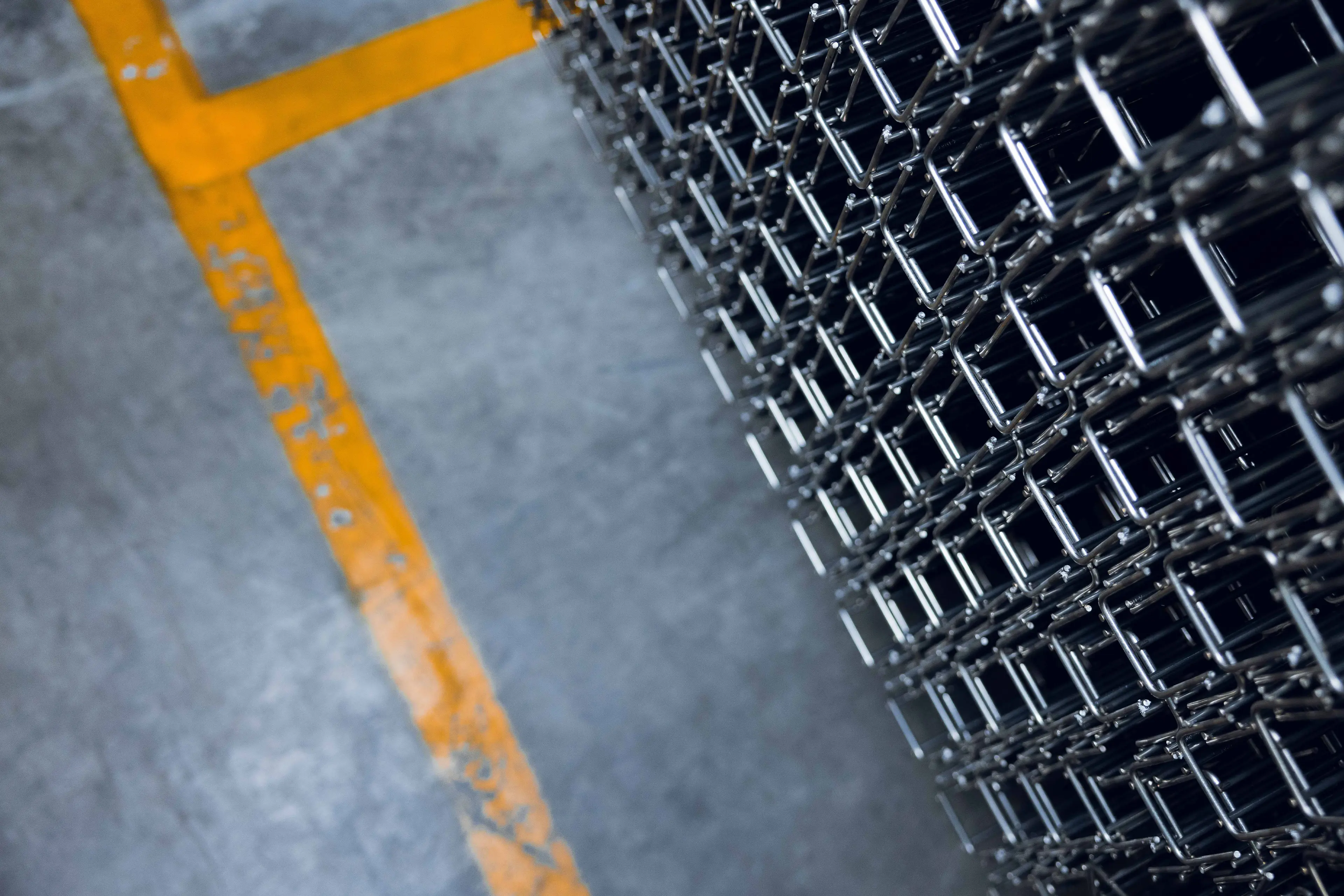
Wire trays with the right corrosion classifications
Depending on the environment and its level of corrosion in which you use our products, there is a need for different surface treatments. Below we have created a corrosion guide with the different corrosion classes, what they mean and when the different surface treatments are needed.
The choice of material and coating is influenced by several factors. Humidity and salt in the air have a major impact, and in some environments there may be substances that significantly shorten the life of the coating. Therefore, it is important to determine the corrosivity and corrosion class according to EN ISO 12944-2 to select the right coating.
What are corrosion classes?
Corrosion classes, formerly known as environmental classes, are a classification of different environments based on the degree of corrosion, or scaling per unit time, that a metal can be expected to be exposed to in a specific environment. These classes are critical for understanding how different metals react in different environments and for adapting protective measures accordingly.
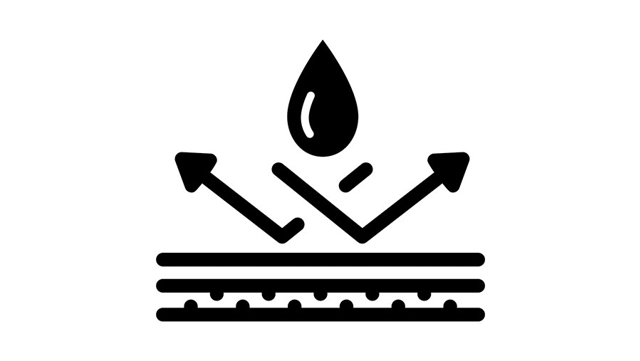
Why are corrosion classes important?
Understanding the corrosivity class of a particular metal in a specific environment is crucial to ensure long-term durability and efficiency. This is particularly important in industrial applications where metal components are exposed to varying, and often demanding, conditions.
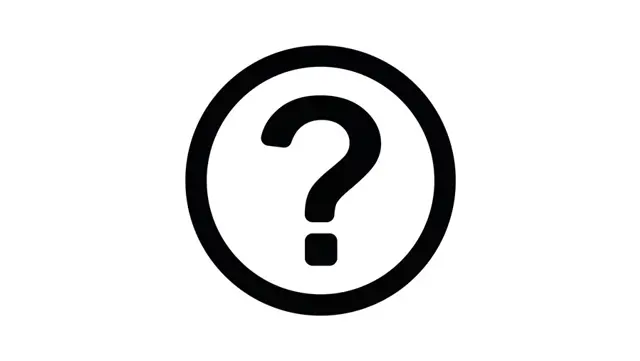
Customization of coating and pre-treatment
Once the corrosivity class of a metal has been determined for a particular environment, the surface treatment and associated pre-treatment can be adapted to optimize protection. This means that the right treatment can be chosen to maximize the lifetime and performance of metal components, which is crucial to minimize maintenance costs and downtime.
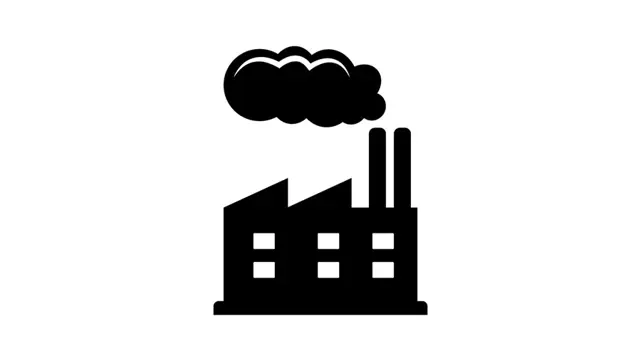
Corrosivity classes and different metals
It is important to note that the corrosivity class is linked to both the environment and the metal, as different metals can react differently to the same environment.
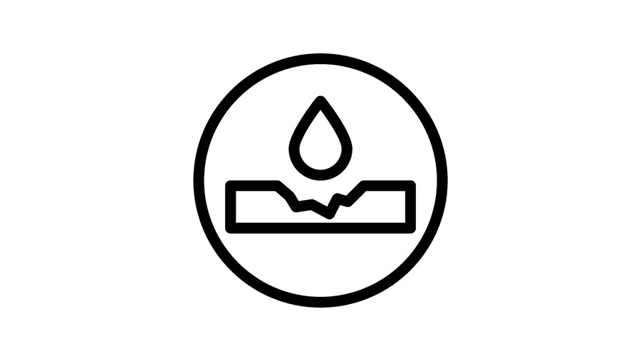
What does EN ISO 12944-2 mean?
EN ISO 12944-2 is an international standard that specifies requirements and guidelines for the protection of steel structures against corrosion by appropriate paint systems. This standard is essential to ensure long-lasting protection and durability of metal components in different environments.
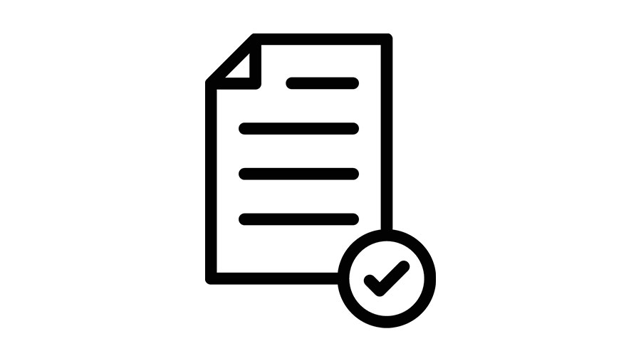
X-Tray covers all corrosion classes
Corrosivity classes according to SS-EN ISO 9223 and SS-EN ISO 12944-2
C1
Very low corrosion environment, e.g. indoors in heated spaces with dry air and insignificant amounts of contaminants. Recommended surface treatments: Electro-galvanising, Sendzimir, hot-dip galvanising, zinc/nickel.
C2
Low corrosivity environment such as unheated indoor spaces with varying temperature and humidity. Also outdoors in low concentrations of air pollution, rural areas. Recommended surface treatments: Sendzimir, hot dip galvanising, zinc/nickel.
C3
Environments with moderate corrosivity. Indoor environments with moderate humidity and some air pollution. Outdoors in moderate amounts of air pollution and urban and light industrial areas. Recommended finishes: Hot dip galvanised, zinc/nickel.
C4
Highly corrosive environment – significant amounts of air pollution in outdoor environments or moderate amounts of salt, industrial and coastal areas. Indoor environment with high humidity and high amounts of air pollution. Recommended finishes: Hot dip galvanised, zinc/nickel, 304L stainless steel.
C5-I
Industrial environment with very high corrosivity. Outdoor industrial areas with harsh climate and high humidity. Coastal and marine areas with large amounts of salt. Permanent moisture condensation in indoor environments and high levels of air pollution. Recommended finishes: 304LK stainless steel and 316L acid-proof steel.
C5-M
Marine environment with very high corrosivity. Outdoor environments such as industrial, coastal and marine areas in subtropical and tropical climates with salt and pollution, shipyard zones. Indoor environments with extreme humidity, condensation and extremely harsh climates. Recommended surface treatment: acid-proof 316L.
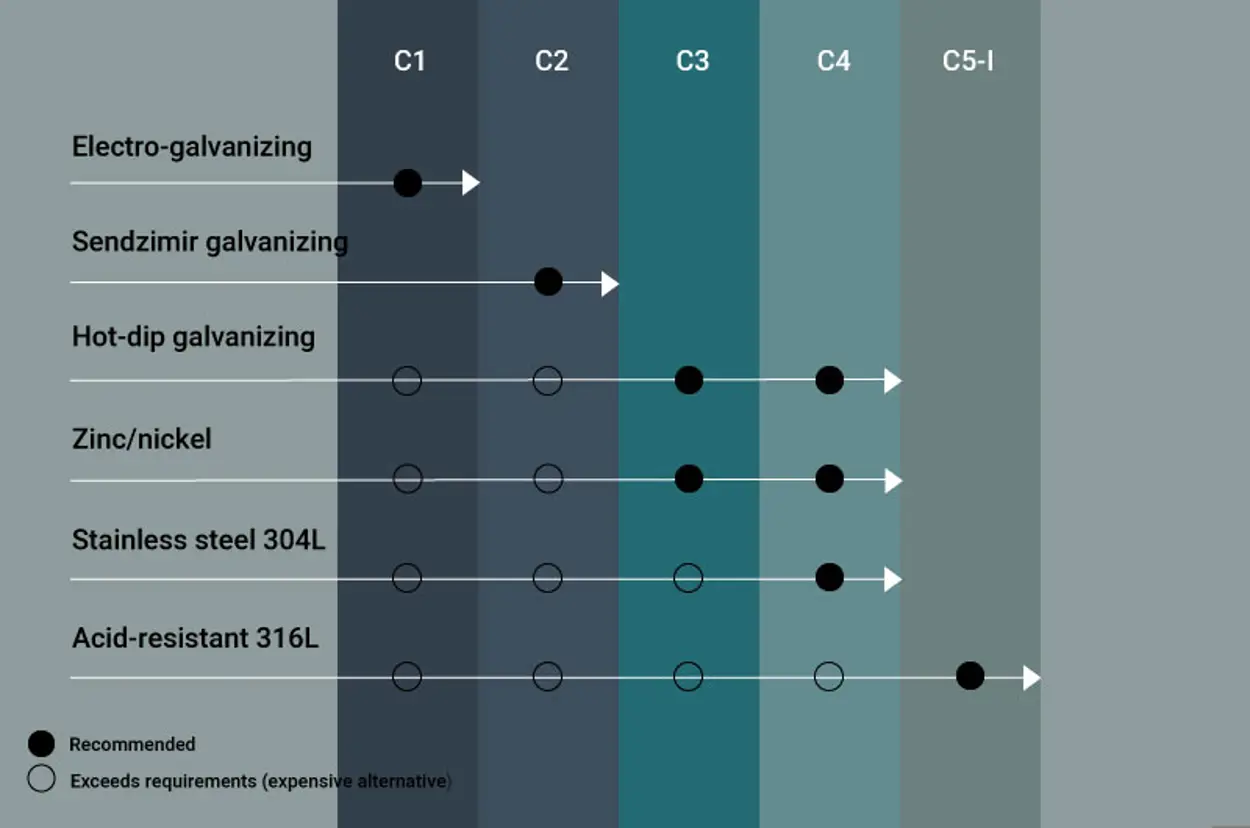
Different coatings and corrosion classes
We have created a guide to help you choose the right material/coating based on the environment in which the product will be used, contributing to a longer product lifetime;
Electro-galvanising
Electro-galvanising involves applying a thin layer of zinc to provide a basic level of protection. This type of treatment is used when appearance is important in a dry indoor environment where protection against corrosion is limited. It is effective for environments with low to moderate corrosivity, corresponding to corrosion classes C1 (very low corrosivity) and C2 (low corrosivity).
According to standards: SS-EN ISO 2081:2008, DIN 50961, DIN-EN 12329
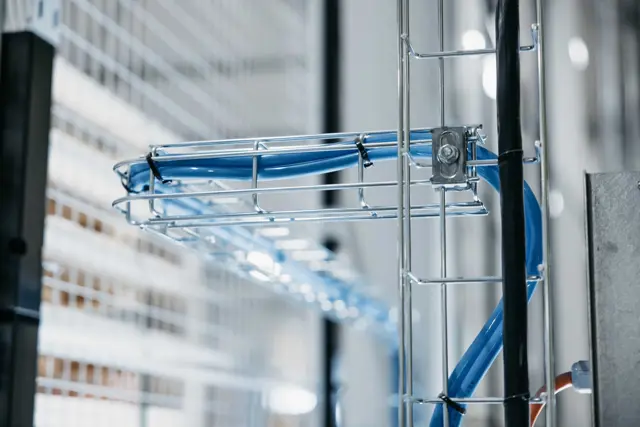
Sendzimir galvanising
Sendzimir galvanising, also known as continuous galvanising and an alternative to hot-dip galvanising, is a process in which steel is coated with zinc by dipping it into a molten zinc bath. This coating is used on materials and products where hot-dip galvanising is not optimal, for example on materials such as sheet metal. Functionality and lifetime are the same. Can be used in situations requiring corrosion protection in moderately corrosive environments, corresponding to C2 (low corrosivity) to C3 (moderate corrosivity).
According to standard: SS-EN 10327:2004
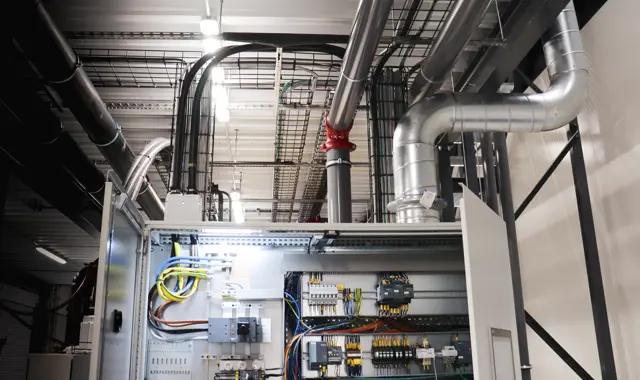
Hot-dip galvanising
Hot-dip galvanising involves dipping the steel in molten zinc, which provides a thicker and more durable protective layer. The treatment gives the product a matt but hard-wearing surface, and to improve aesthetics it is recommended that the product is painted. If damage occurs to the surface, the zinc has the ability to repair itself through ionisation.
This finish is ideal for higher corrosivity, including outdoor and industrial environments. This surface treatment corresponds to corrosivity classes C3 (moderate corrosivity) to C4 (high corrosivity).
According to standards: SS-EN ISO 1461:2009, DIN 50976
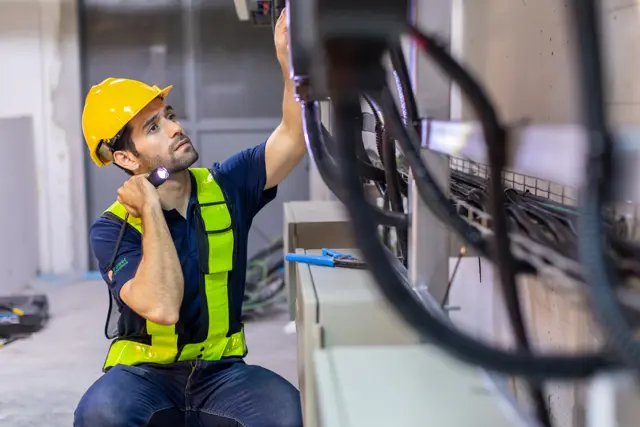
Zinc/nickel
Zinc/Nickel is a thin alloy containing 12-15% nickel and has the same properties as hot-dip galvanised and is used on products where hot-dip galvanising is not possible or does not provide optimal protection. It is used on many of the products and accessories where it is important that tight tolerances are maintained, e.g. for screws and nuts.
The coating is widely used in the automotive industry and other demanding environments, and it corresponds to corrosivity classes C3 (moderate corrosivity) to C4 (high corrosivity).
According to standards: SS-EN ISO 11997-1, DIN 50979
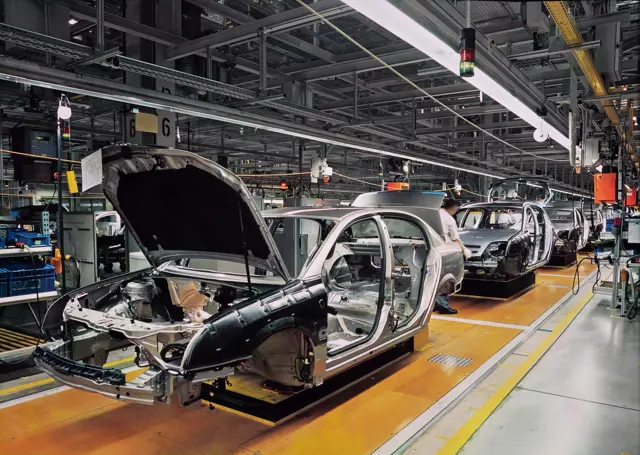
Stainless steel 304L
Stainless steel 304L has high corrosion resistance due to its high chromium and nickel content. It is suitable for use in corrosion classes C4 (high corrosivity) to C5-I (very high corrosivity) and is widely used in building construction and food industry.
According to standard: SS 2352 / AISI 304L
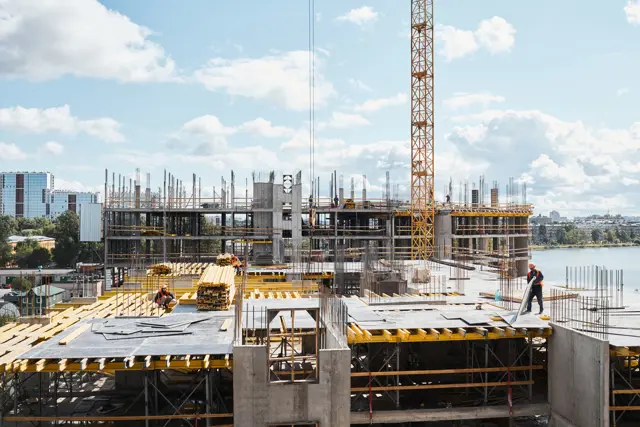
Acid-resistant 316L
The material is 316L, EN 1.4404, and is dipped in an acid bath with the addition of molybdenum, creating an impurity-free surface that is easy to clean and increased corrosion resistance. It is ideal for very demanding environments, including marine environments and industries with chemical exposure, corresponding to corrosion classes C5-I and C5-M (extremely high corrosivity).
According to standard: SS 2348 SF / AISI 316L
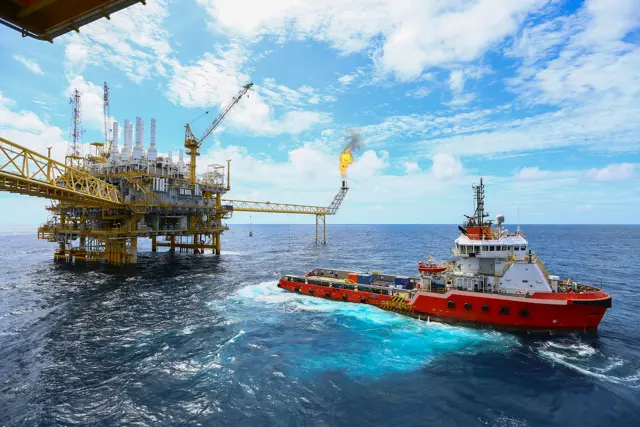
Ask us
We guide you through the different corrosion classes and help you choose the right coating for your products to optimize their lifetime.
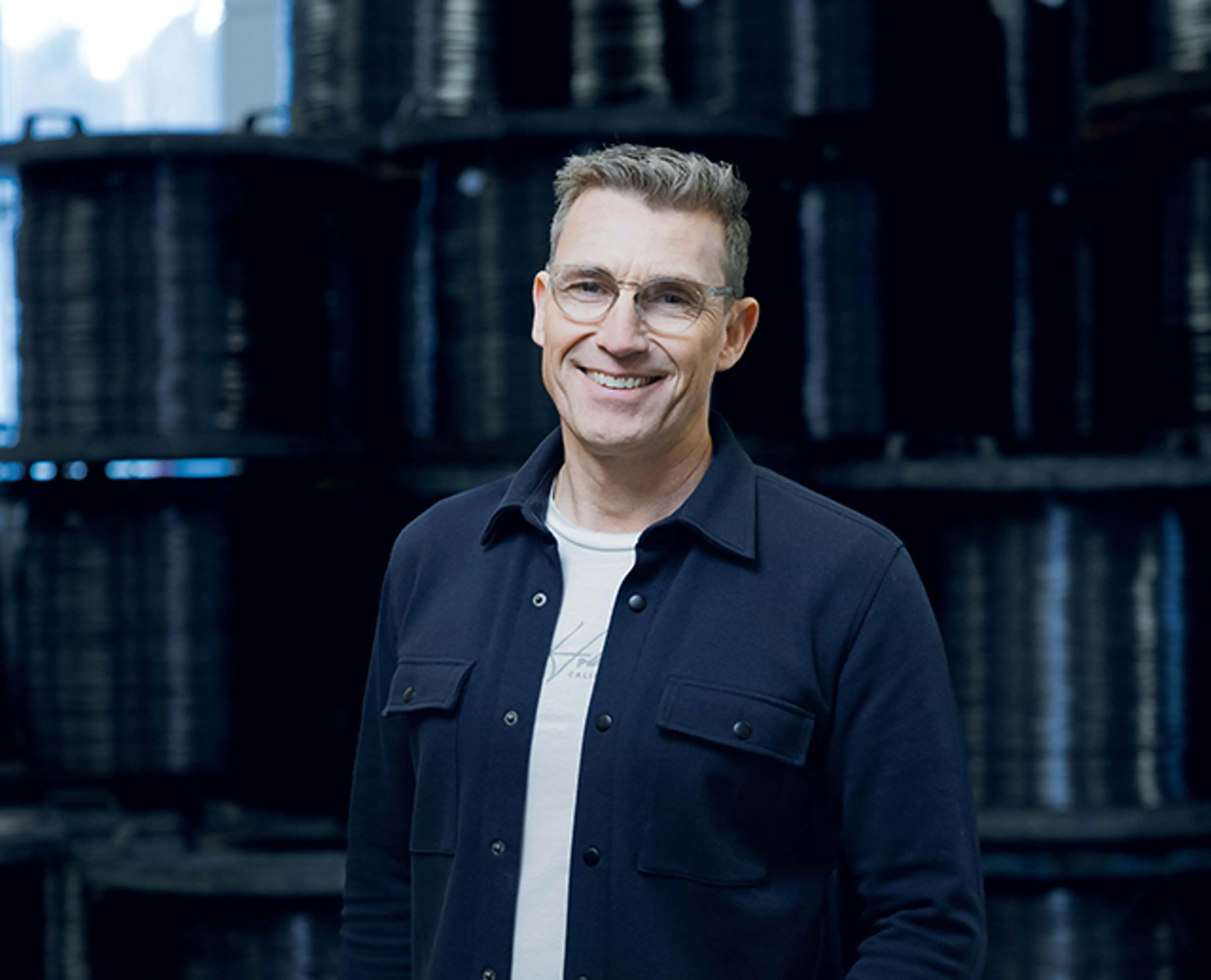
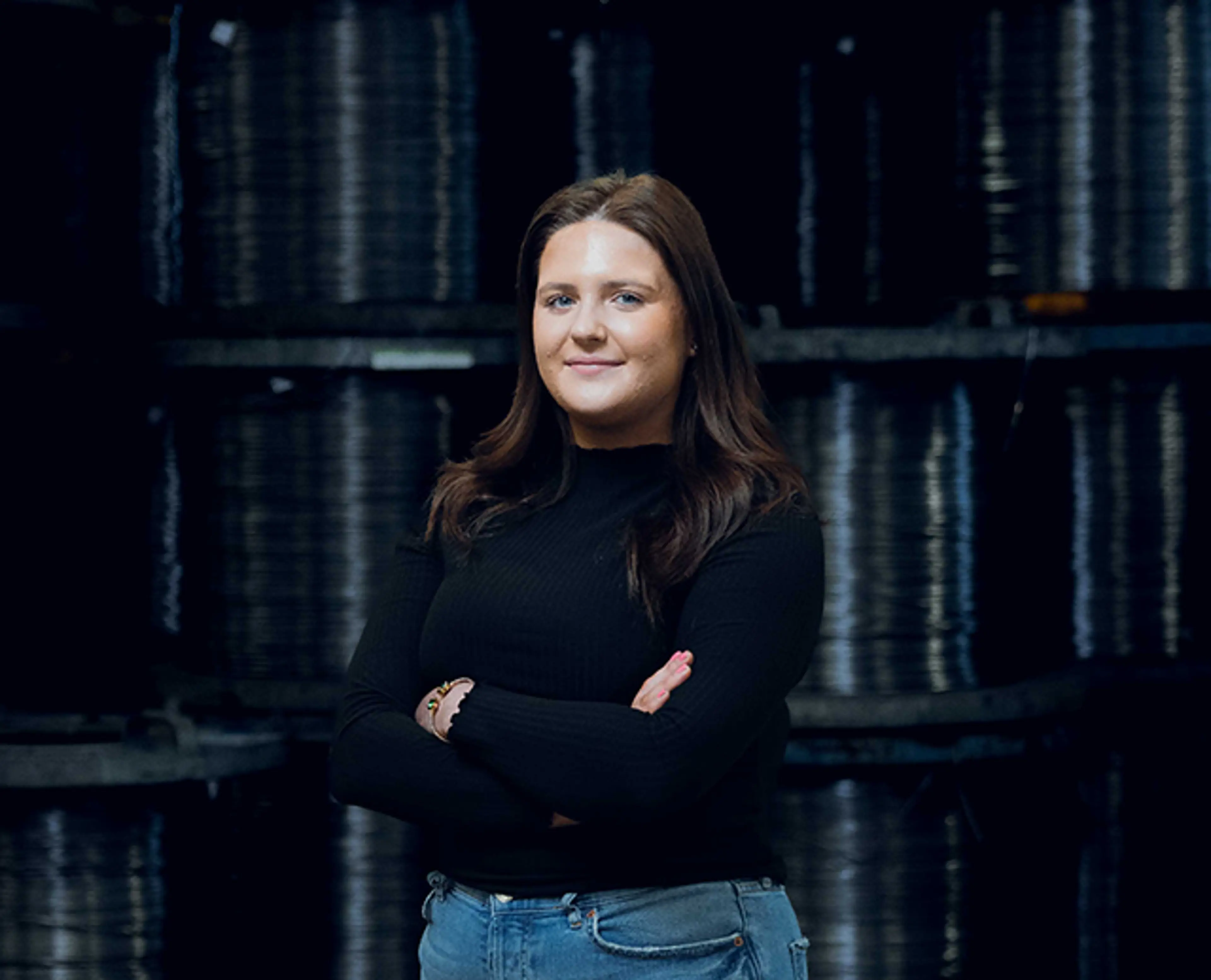